Ceramic Coatings
Chemical Vapor Deposition
Figure 5 illustrates the basic CVD process in more detail. All rate limiting steps are given. Reactants are brought in the gas phase, usually by evaporation, they dissociate near and on the surface of the product and react with each other and so form a coating. The dissociation and subsequent reaction can be accomplished by high(er) temperatures, or by a plasma. In the first case the coating is usually being applied in a furnace, and is referred to as thermal CVD. The latter case is referred to as plasma (assisted) CVD.
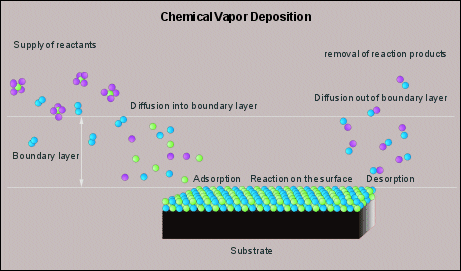
(Fig 5, Schematic representation of CVD, dissociation and subsequent
reaction occur due to high(er) temperatures. Click on the image to get it enlarged).
Newer CVD techniques employ a laser to dissociate and provide the energy for the formation reaction. Furthermore there is a distinction between Low Pressure Chemical Vapor deposition (LP-CVD) and atmospheric pressure CVD (AP-CVD). Each technique results in different coating properties (although the material deposited is the same).The difficult task in CVD is finding the right process parameters which ensure a homogeneous reaction zone, meaning even layer thickness and coating composition over the entire product. Most important parameters are:
- reactants concentrationgas
- flows temperature
- reactor pressure
An advantage of CVD over PVD (physical vapor deposition) is the fact that with CVD it is easy to coat products internally. Figure 6 shows a nanostructured fractal coating of TiO2.
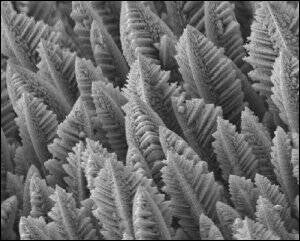
(Fig 6, nanostructured fractal coating of TiO2)